Ve světě průmyslové recyklace se výkon měří v mikronech a tunách za hodinu. Pro provozovatele recyklačních zařízení v USA a Evropě závisí ziskovost zpracovatelské linky často na efektivitě a spolehlivosti jejích strojů. Jádrem každého průmyslového drtiče je jeho nejdůležitější součást: rotor. Je srdcem stroje a jeho konstrukce určuje vše od výstupní rychlosti až po kvalitu konečného produktu.
Ne všechny rotory jsou si však rovny. Konstrukce, která vyniká při zpracování PET lahví, může mít potíže s LDPE fólií a rotor, který drtí objemné HDPE sudy, může při manipulaci s křehkými materiály produkovat nadměrné jemné částice. Pro osoby s rozhodovací pravomocí a technické odborníky není pochopení složitého vztahu mezi konstrukcí rotoru, drticí kapacitou a uniformitou částic jen akademickým cvičením – je zásadní pro optimalizaci provozu a maximalizaci návratnosti investic.
V této komplexní analýze společnost Energycle Machine využije desítky let inženýrských zkušeností k analýze klíčových konstrukcí rotorů, vyhodnocení jejich výkonu v různých aplikacích a poskytnutí informací, které potřebujete k informovanému rozhodnutí pro vaše zařízení.
Pochopení základních metrik: Propustnost a uniformita
Co je to propustnost?
Propustnost, často měřená v kilogramech nebo tunách za hodinu, je rychlost, s jakou drtič dokáže zpracovat daný materiál. Vyšší propustnost znamená více zpracovaného materiálu za kratší dobu, což má přímý dopad na provozní kapacitu a příjmy. Skutečná efektivita však nespočívá jen v rychlosti. Jde o dosažení vysoké propustnosti konzistentně, bez neplánovaných prostojů, přetížení motoru nebo nadměrné spotřeby energie.
Proč je důležitá uniformita částic?
Jednotnost částic označuje konzistenci velikosti a tvaru drceného materiálu (drceného nebo vločkového). Jednotná velikost částic je zásadní z několika důvodů, včetně lepšího výkonu v následném zpracování, jako jsou prací linky a extrudéry, a dosažení vyšší ceny za konečný recyklovaný produkt.
Srovnávací analýza: Konstrukce klíčových rotorů
Na trhu s drtiči s jedním hřídelem se dva typy konstrukcí staly průmyslovými archetypy: rotor V-Cut (nebo Chevron) a stupňovitý rotor (neboli Staggered).
Rotor V-Cut (Chevron)
Jak název napovídá, rotor V-Cut uspořádá své nože podél hřídele do souvislého tvaru „V“. Tato konstrukce je navržena tak, aby vytvářela hladký, nůžkový řezný pohyb proti stacionárním protinožům, čímž přirozeně přitahuje materiál směrem ke středu řezací komory. Tím se rovnoměrně rozloží řezná zátěž, sníží se výkonové špičky a zajistí se tišší a plynulejší provoz.
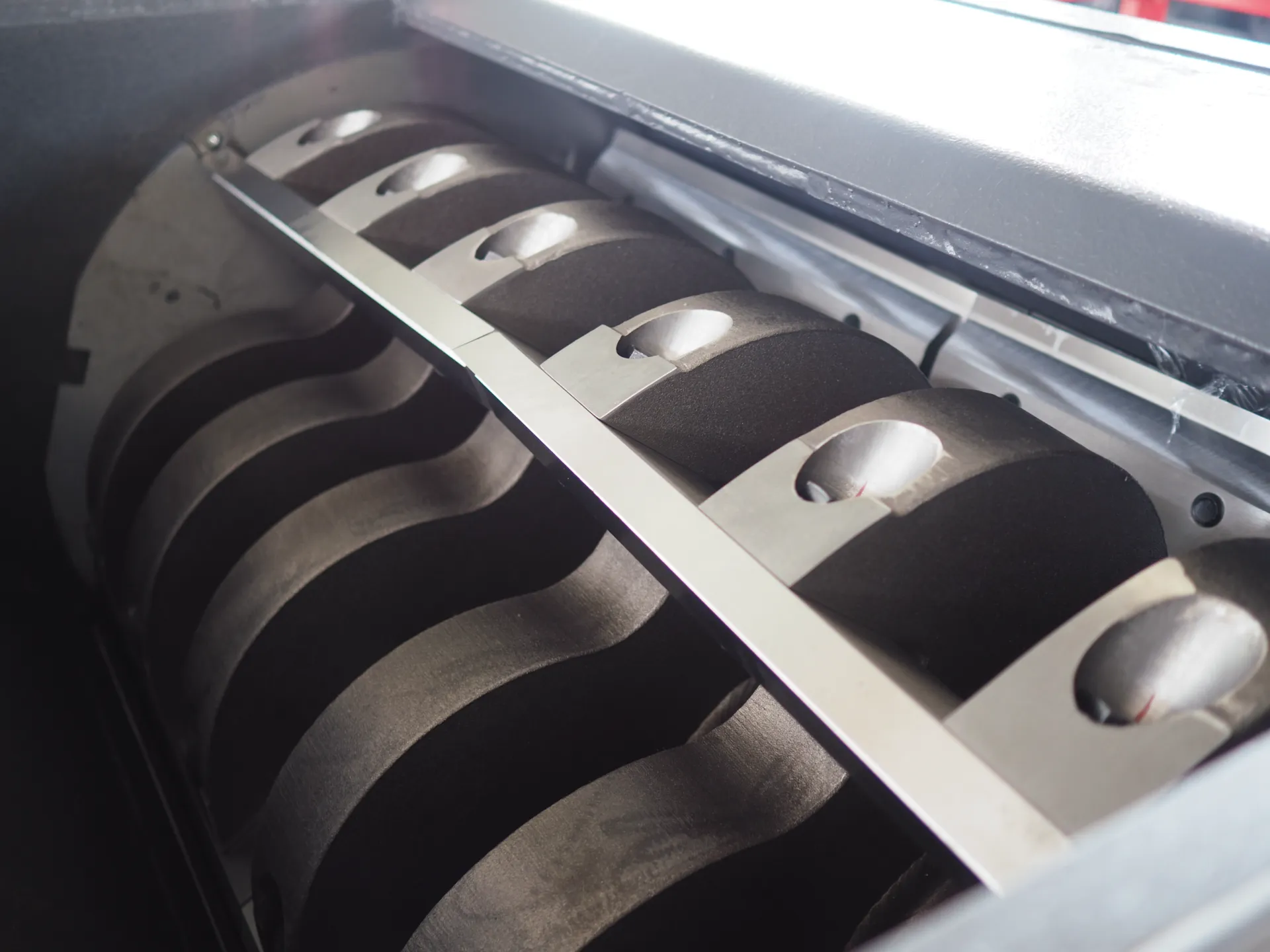
Standardní konstrukce V-Cut je sice vysoce účinná, ale někdy může být méně účinná při uchopení a drcení velmi velkých nebo objemných předmětů. Právě zde naše kompletní řada vysoce výkonných průmyslových drtičů V Energycle Machine přichází na řadu návrhy, které byly zdokonaleny tak, aby překonaly tato tradiční omezení.
Stupňovitý rotor
Schovaný rotor zaujímá odlišný filozofický přístup. Jeho nože jsou uspořádány v odděleném, odsazeném vzoru, což vytváří agresivnější, drtící účinek. Každý nůž funguje jako samostatný bod nárazu, který děruje a trhá materiál. To je vysoce účinné při drcení velkých, hustých předmětů, jako jsou HDPE sudy a průmyslové odpady.
Hybridní rotor: Inovativní přístup společnosti Energycle Machine
S vědomím, že žádný konkrétní design není ideální pro každou aplikaci, vyvinul tým inženýrů společnosti Energycle Machine řadu hybridních rotorových konstrukcí. Naším cílem je spojit plynulou účinnost V-Cut s agresivním výkonem stupňovitého rotoru a vytvořit tak všestranné řešení. Naše patentované konstrukce, které se objevují v... Řada Energycle ERMSD, často zahrnují upravený V-Cut vzor se speciálně profilovanými, stupňovitě uspořádanými noži, aby poskytovaly robustní výkon, kterému naši klienti v USA a Evropě důvěřují.
Srovnání výkonu v kostce
Typ materiálu | V-Cut rotor | Střídavý rotor | Hybridní rotor Energycle |
---|---|---|---|
LDPE fólie | Vynikající | Veletrh | Vynikající |
PET lahve | Vynikající | Dobrý | Vynikající |
HDPE sudy | Veletrh | Vynikající | Vynikající |
Proplachování z tvrdého plastu | Veletrh | Vynikající | Vynikající |
Často kladené otázky (FAQ)
Mohu použít jeden drtič na více druhů plastů?
Ano. Právě zde skutečně vyniká všestranná konstrukce rotoru, jako je hybridní rotor Energycle Machine. Je navržen tak, aby poskytoval vynikající výkon v široké škále materiálů, od měkkých fólií až po tvrdé plasty, což vašemu provozu dává větší flexibilitu.
Jak otáčky rotoru ovlivňují výkon drcení?
Nižší otáčky rotoru (obvykle 70–90 ot./min. u drtičů s jednou hřídelí) generují vyšší točivý moment, což je ideální pro řezání houževnatých materiálů. Snižují také tvorbu tepla, minimalizují jemné částice a snižují provozní hluk. Vyšší otáčky mohou zvýšit průchodnost surovin u velmi lehkých materiálů, ale často jsou za cenu vyššího opotřebení a nižší kvality řezu.
Jak často je třeba vyměňovat nože rotoru?
To do značné míry závisí na zpracovávaném materiálu a provozních hodinách. S vysoce kvalitními a správně udržovanými noži od Energycle Machine naši klienti obvykle dosahují tisíců hodin provozní životnosti. Naše drtiče jsou navrženy pro snadný přístup, aby otáčení a výměna nožů byly co nejjednodušší.
Jste připraveni optimalizovat výkon drcení?
Kontaktujte ještě dnes technický tým Energycle Machine a získejte bezplatnou konzultaci a analýzu zpracování materiálu. Pomůžeme vám najít perfektní řešení pro rozvoj vašeho podnikání.
Žádost o konzultaci