Der erste und wichtigste Schritt beim Recycling hochwertiger Kunststoffe. Entwickelt für Langlebigkeit, Effizienz und maximale Betriebszeit.
Angebot anfordernWarum sollten Sie sich für den Plastikflaschenzerkleinerer von Energycle entscheiden?
Drehmomentstarke Leistung
Ausgestattet mit importierten Markenmotoren für niedrigen Energieverbrauch und leistungsstarke, konstante Leistung.
Klingen aus gehärtetem Stahl
Verwendet DC53/SKD11-Legierungsstahl, der überragende Härte, Zähigkeit und Verschleißfestigkeit für eine längere Lebensdauer bietet.
Einfache Wartung
Verfügt über externe Lager und leicht abnehmbare Verschleißschutzplatten, was die Wartung vereinfacht und Ausfallzeiten reduziert.
Effiziente V-Cut-Technologie
Die standardmäßige V-förmige Schnittgeometrie verbessert die Recyclingeffizienz und reduziert den Staubgehalt im Endprodukt.
Von der Abfallflasche zur wertvollen Flocke
Unsere Maschine vereinfacht die komplexe Aufgabe des Kunststoffrecyclings und verwandelt sie in einen rationalisierten, automatisierten Prozess.
1. Füttern
Die Abfallflaschen werden über ein Förderband in den Trichter geladen.
2. Zerkleinern
Rotierende Klingen in der Schneidkammer zerkleinern das Material in kleinere Stücke.
3. Screening
Ein Siebgewebe bestimmt die endgültige Flockengröße und sorgt für Gleichmäßigkeit.
4. Entladung
Gleichmäßige Flocken werden ausgetragen, bereit für eine vollständige PET-Flaschen-Recyclingsystem.
Für Spitzenleistungen entwickelt
Hochleistungsrotor
Ein dynamisch ausgewuchteter, hochbelastbarer Rotor aus geschweißter Stahlkonstruktion sorgt für einen stabilen, vibrationsfreien Betrieb auch bei zähen Materialien.
Präzisionsmesserklingen
DC53-Stahlklingen bieten im Vergleich zum Standard D2/SKD11 die doppelte Robustheit und überlegene Verschleißfestigkeit und gewährleisten so einen sauberen Schnitt und eine lange Lebensdauer.
Verstärkte Brechkammer
Die aus einer Stahlplatte mit ultrahoher Härte (40 mm) geschweißte Kammer ist verschleißfest und langlebig und kann problemlos mit anspruchsvollen Materialien umgehen.
Erweiterte Sicherheitskontrollen
Ausgestattet mit einem Motorstrom-Überlastungsschutz und einem Sicherheitsendschalter, der den Start verhindert, wenn die Abdeckung 100% nicht geschlossen ist.
Technische Spezifikationen
Modell | Rotordurchmesser (mm) | Rotorbreite (mm) | Kapazität (kg/h) | Motorleistung (kW) | Anzahl der Statormesser |
---|---|---|---|---|---|
ERM-600-CRPET | 600 | 700 | ~500 | 22-30 | 5*2 |
ERM-800-CRPET | 800 | 1000 | 800-1000 | 37-45 | 5*2 oder 7*2 |
ERM-1000-CRPET | 1000 | 1200 | ~1500 | 55-75 | 5*2 oder 7*2 |
ERM-1200-CRPET | 1200 | 1600 | 2000-2500 | 75-90 | 5*4 oder 7*4 |
Sehen Sie es in Aktion
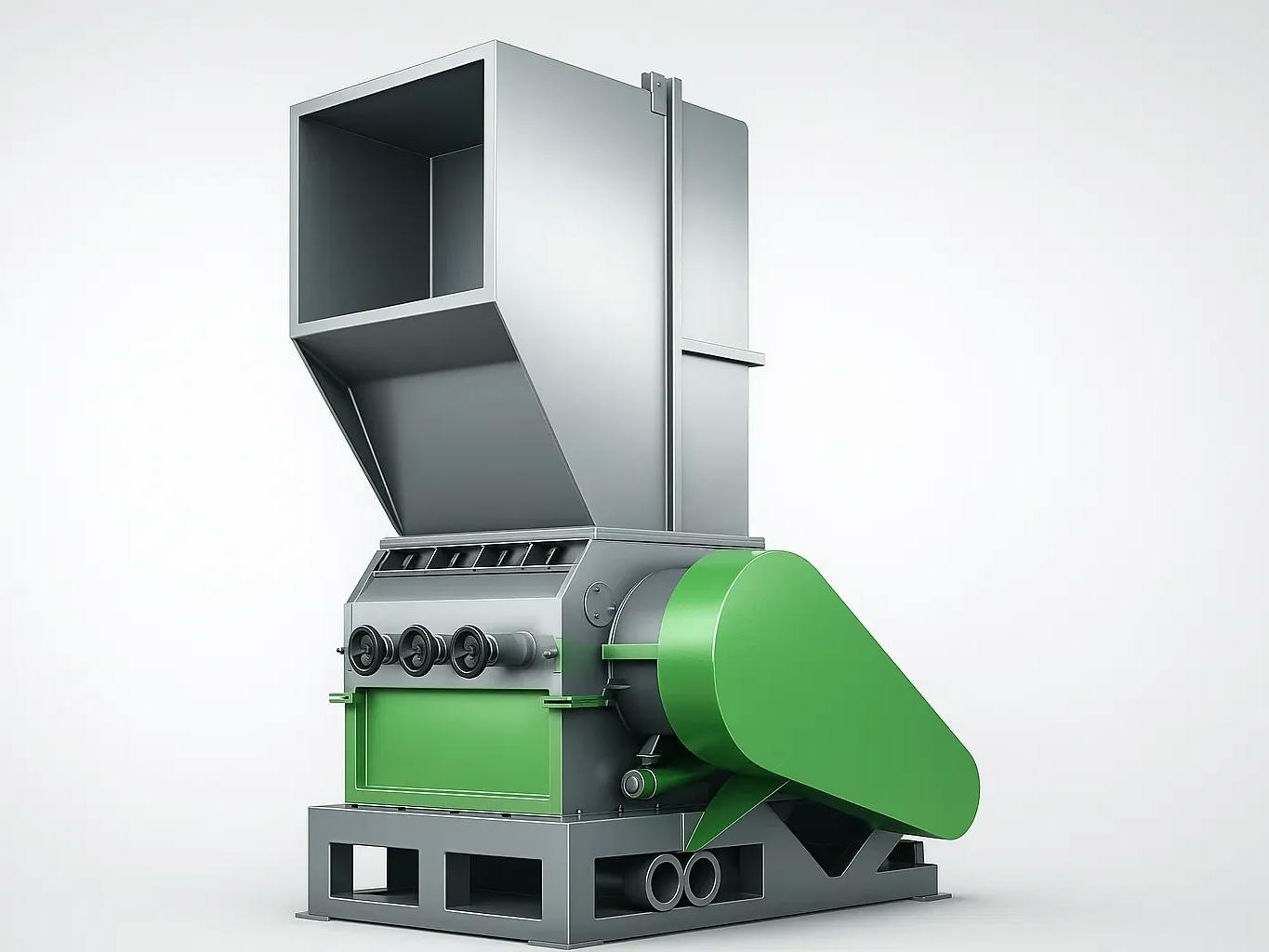
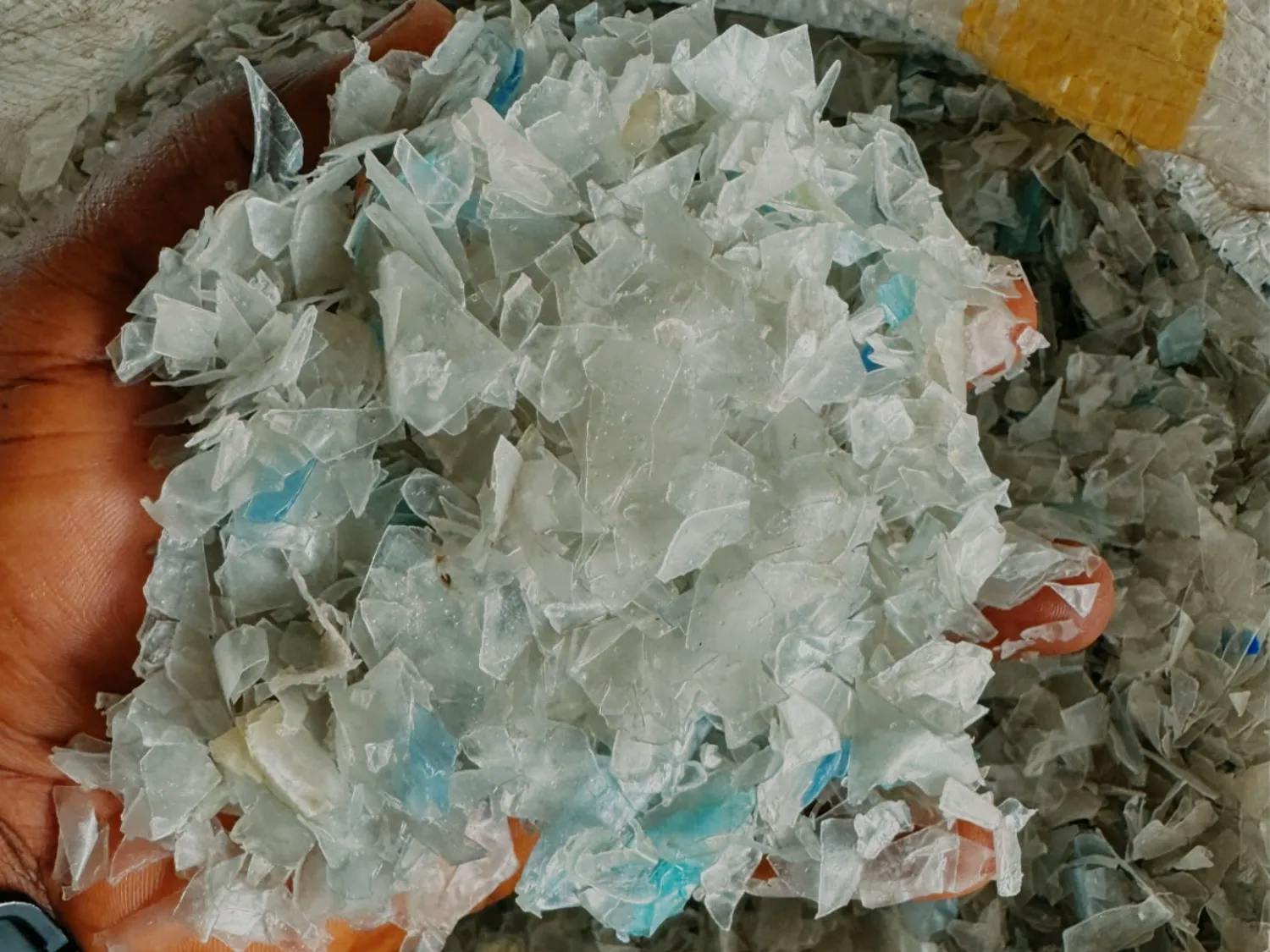
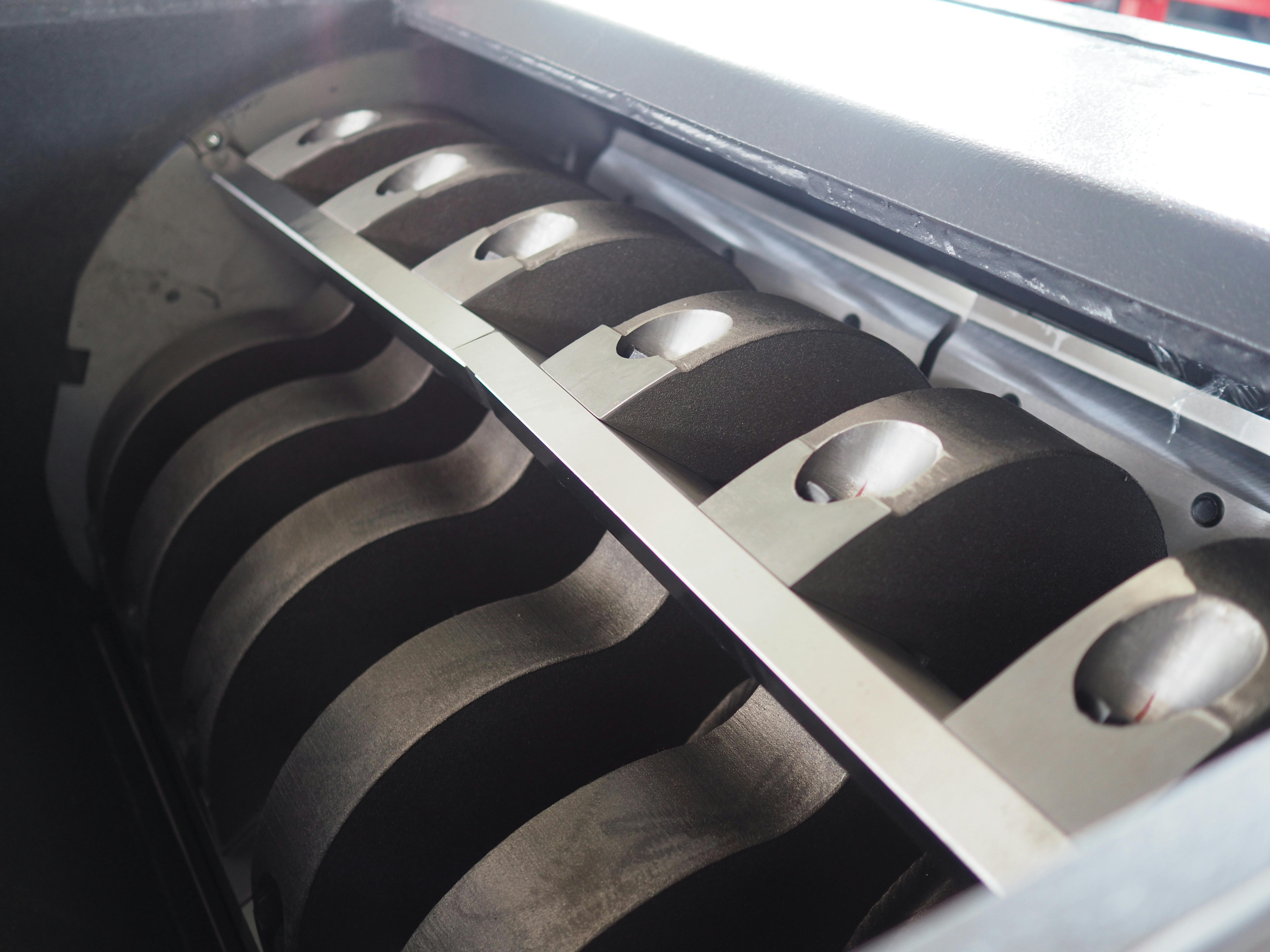
Fordern Sie eine individuelle Lösung und ein Angebot an
Unser Team unterstützt Sie gerne bei der Auswahl der perfekten Maschinenkonfiguration für Ihre spezifischen Anforderungen. Kontaktieren Sie uns noch heute für eine unverbindliche Beratung und detaillierte Preisinformationen.
Häufig gestellte Fragen
Die RM-Serie ist primär für PET-Flaschen konzipiert, ist aber äußerst vielseitig. Mit der entsprechenden Rotor- und Siebkonfiguration lassen sich auch andere Materialien wie PP/PE-Behälter, Hartplastikflaschen, Chemikalienfässer, Spritzgussteile und Kunststofffolien effizient verarbeiten.
Die endgültige Flockengröße wird durch die austauschbare Siebmaschenweite bestimmt. Wir bieten verschiedene Siebgrößen an, um Ihren spezifischen Anforderungen gerecht zu werden. Für Kunststoffflaschen reichen die Maschenweiten typischerweise von 10 mm bis 20 mm.
Dieser Brecher ist eine wichtige Komponente, die als eigenständige Einheit zur Größenreduzierung eingesetzt werden kann. Er ist jedoch auch so konzipiert, dass er sich nahtlos in unser komplettes PET-Flaschen-Recyclingsystem, das Wasch-, Trocknungs- und Pelletierungsschritte umfasst, um hochwertige wiederverwendbare Materialien herzustellen.
Unsere Klingen bestehen aus hochwertigem DC53- oder SKD11/D2-Legierungsstahl und bieten so höchste Verschleißfestigkeit. Die Lebensdauer der Klinge hängt vom zu verarbeitenden Material ab. Der modulare Aufbau und die verstellbaren Rotorwerkzeuge ermöglichen jedoch einen schnellen und einfachen Austausch und minimieren so Ausfallzeiten.
Ja, wir bieten umfassende Dienstleistungen an, darunter technische Beratung vor dem Kauf, Installation und Inbetriebnahme im Ausland sowie Kundendienst und Fehlerbehebung rund um die Uhr. Wir sorgen dafür, dass Ihre Maschine mit maximaler Leistung läuft.