Entdecken Sie die transformative Kraft der Vertikale Misch- und Trocknungsmaschine, ein innovatives und vielseitiges Industriegerät, das Ihre Fertigungsprozesse revolutioniert. Dieses fortschrittliche System integriert nahtlos wichtige Misch- und Trocknungsfunktionen und ist damit ein unverzichtbarer Bestandteil einer Vielzahl von Branchen. Ob Sie Feinchemikalien, Lebensmittelzutaten, Pharmazeutika oder Kosmetika verarbeiten – diese Maschine steigert die Effizienz, gewährleistet höchste Produktqualität und optimiert Ihre Abläufe.
Entdecken Sie die wichtigsten Funktionen und Vorteile
Hauptmerkmale: Förderung hervorragender Verarbeitung
1. Intelligentes vertikales Design: Die Maschine verfügt typischerweise über einen hochentwickelten vertikalen, zylindrischen Tank, oft mit konischem Boden. Dieses intelligente Design fördert einen hocheffizienten Materialfluss, eine gründliche Durchmischung und eine gleichmäßige Trocknung. Die vertikale Ausrichtung reduziert den Platzbedarf der Anlage erheblich und macht sie zur idealen Lösung für Anlagen mit begrenztem Platzangebot. Gleichzeitig erleichtert sie die Schwerkraftentleerung und vereinfacht die Reinigung.
2. Hochwertige Baumaterialien: Die sorgfältige Fertigung aus hochwertigem Edelstahl (z. B. SS304, SS316L) oder anderen speziellen korrosionsbeständigen Legierungen garantiert außergewöhnliche Langlebigkeit und robuste Beständigkeit gegen eine Vielzahl von Chemikalien. Dadurch eignet sie sich perfekt für anspruchsvolle Industrieumgebungen und gewährleistet die Einhaltung strenger Hygienestandards, einschließlich der GMP-Anforderungen in pharmazeutischen Anwendungen.
3. Fortschrittliche Heiz- und Trocknungssysteme: Viele Vertikalmischer sind mit hochentwickelten integrierten Heizsystemen wie Doppelmantelheizung/-kühlung oder Heißluftzirkulation ausgestattet. Diese Systeme ermöglichen eine präzise Temperaturregelung sowohl während der Misch- als auch der Trocknungsphase, was für die Verarbeitung temperaturempfindlicher Materialien und das effiziente Erreichen des gewünschten Feuchtigkeitsgehalts entscheidend ist.
4. Intuitives Steuerungssystem: Ausgestattet mit hochmodernen Bedienfeldern, oft mit SPS-Steuerung und benutzerfreundlicher Mensch-Maschine-Schnittstelle (HMI). So können Bediener verschiedene kritische Parameter wie Temperatur, Mischgeschwindigkeit, Verarbeitungszeit und Vakuumniveau einfach einstellen, überwachen und anpassen. Diese Kontrollmöglichkeit erhöht die Betriebspräzision, gewährleistet die Wiederholbarkeit von Charge zu Charge und vereinfacht die Prozessvalidierung.
5. Umfassende Sicherheitsfunktionen: Die Sicherheit von Bediener und Ausrüstung hat oberste Priorität. Diese Maschinen verfügen üblicherweise über wichtige Sicherheitsmechanismen wie Not-Aus-Schalter, Sicherheitsverriegelungen an Zugangstüren und -klappen, Überlastschutz für Motoren und Überdruckventile, die eine sichere Betriebsumgebung gewährleisten.
6. Vielseitiges Zubehör und Anpassungsmöglichkeiten: Die Funktionalität lässt sich durch verschiedene optionale Anbaugeräte deutlich erweitern. Dazu gehören Sprühdüsen zur Flüssigkeitszugabe oder Granulierung, Vakuumsysteme zur Entlüftung und Niedertemperaturtrocknung, Probenahmeöffnungen für prozessbegleitende Qualitätskontrollen und Wägezellen für präzises Wiegen. Wir bieten kundenspezifische Konfigurationen für spezifische Materialeigenschaften, Chargengrößen und Betriebsanforderungen.
Technische Parameter (Beispielkonfiguration)
Parameter | Spezifikation |
---|---|
Volumen | 3000 Liter |
Leistung | 4 kW |
Heizleistung | 42 kW |
Lüfter oder Gebläse | 2,2 kW |
Plattendicke | 2,5 mm |
Spindelspezifikationen | φ60×4 |
Klingenstärke | 3 mm |
Schneckendurchmesser | φ273 |
Gewicht der Ausrüstung | 700 kg |
Abmessungen (L x B x H) | 1900 mm x 2300 mm x 3100 mm |
Vielfältige Anwendungen in verschiedenen Branchen:
Chemische Industrie
Ideal zum Mischen und Trocknen verschiedener chemischer Verbindungen, einschließlich Pulver, Granulaten, Pigmenten, Harzen, Katalysatoren und Spezialchemikalien. Sorgt für gründliches Mischen, gleichmäßige Partikelgröße und präzise Feuchtigkeitsentfernung, die für chemische Reaktionen und Produktstabilität entscheidend sind.
Lebensmittel und Getränke
Geeignet zum schonenden und dennoch effektiven Mischen und Trocknen von Gewürzen, Getränkepulvern, Kaffeebohnen, Teeblättern, Backzutaten, Granulaten und anderen Lebensmitteln. Optimiert durch kontrollierte Feuchtigkeitsreduzierung die gewünschte Konsistenz, homogenen Geschmack und verlängerte Haltbarkeit.
Pharmazeutika
Wird häufig für die homogene Mischung von pharmazeutischen Wirkstoffen (APIs) mit Hilfsstoffen, die Herstellung von Granulaten für die Tablettierung und die Trocknung pharmazeutischer Pulver eingesetzt. Gewährleistet gleichbleibende Chargenqualität, gleichmäßige Dosierung und die Einhaltung strenger pharmazeutischer Standards.
Kosmetik und Körperpflege
Wird zum Mischen verschiedener Pulver, Pigmente und Granulate verwendet, die in Kosmetikprodukten wie Gesichtspuder, Talkumpuder und Farbkosmetik verwendet werden. Sorgt für eine gleichmäßige Textur, Farbkonsistenz und die gewünschten Fließeigenschaften des Endprodukts.
Weitere Branchen: Unsere vertikalen Misch- und Trocknungsmaschinen finden auch Anwendung in der Kunststoffe und Polymere Sektor (zum Trocknen von Pellets und Pulvern), Mineralien und Metallurgie (zum Trocknen von Erzen und Feinmineralien) und Landwirtschaftliche Produkte (zur Futter- und Düngemittelverarbeitung).
Vorteile unserer vertikalen Misch- und Trocknungsmaschine:
• Verbesserte Betriebseffizienz: Optimieren Sie Ihren Produktionsablauf durch die nahtlose Kombination von Misch- und Trocknungsprozessen in einer einzigen, integrierten Einheit. Dies reduziert den Materialtransport erheblich, minimiert Prozessschritte und steigert den Gesamtdurchsatz.
• Überlegene Produktqualitätskontrolle: Erreichen Sie eine unvergleichliche Produktkonsistenz durch die schonende und dennoch gründliche Mischwirkung unserer Maschine. Dies gewährleistet eine gleichmäßige Partikelverteilung, homogene Mischungen und einen präzisen Feuchtigkeitsgehalt, entscheidend für Branchen, in denen die Zusammensetzung direkten Einfluss auf Leistung und Qualität hat.
• Erhebliche Energieeinsparungen: Reduzieren Sie Ihre Betriebskosten mit unserem energieeffizienten Design. Merkmale wie fortschrittliche Isolierung, optimierte Heizsysteme und effizienter Motoreinsatz tragen zu einem geringeren Energieverbrauch über die gesamte Lebensdauer der Maschine bei.
• Platzsparende Standfläche: Das intelligente vertikale Design benötigt im Vergleich zu herkömmlichen horizontalen Misch- und Trocknungsalternativen deutlich weniger Stellfläche. Dadurch wird Ihre wertvolle Produktionsfläche optimal genutzt und eine effizientere Anlagengestaltung ermöglicht.
• Reduziertes Kontaminationsrisiko und einfache Wartung: Das geschlossene Systemdesign minimiert das Risiko externer Verunreinigungen und Produktverluste. Glatte Innenflächen und strategisch platzierte Zugangspunkte vereinfachen Reinigung und Wartung, was bei sensiblen Anwendungen entscheidend ist und Ausfallzeiten reduziert.
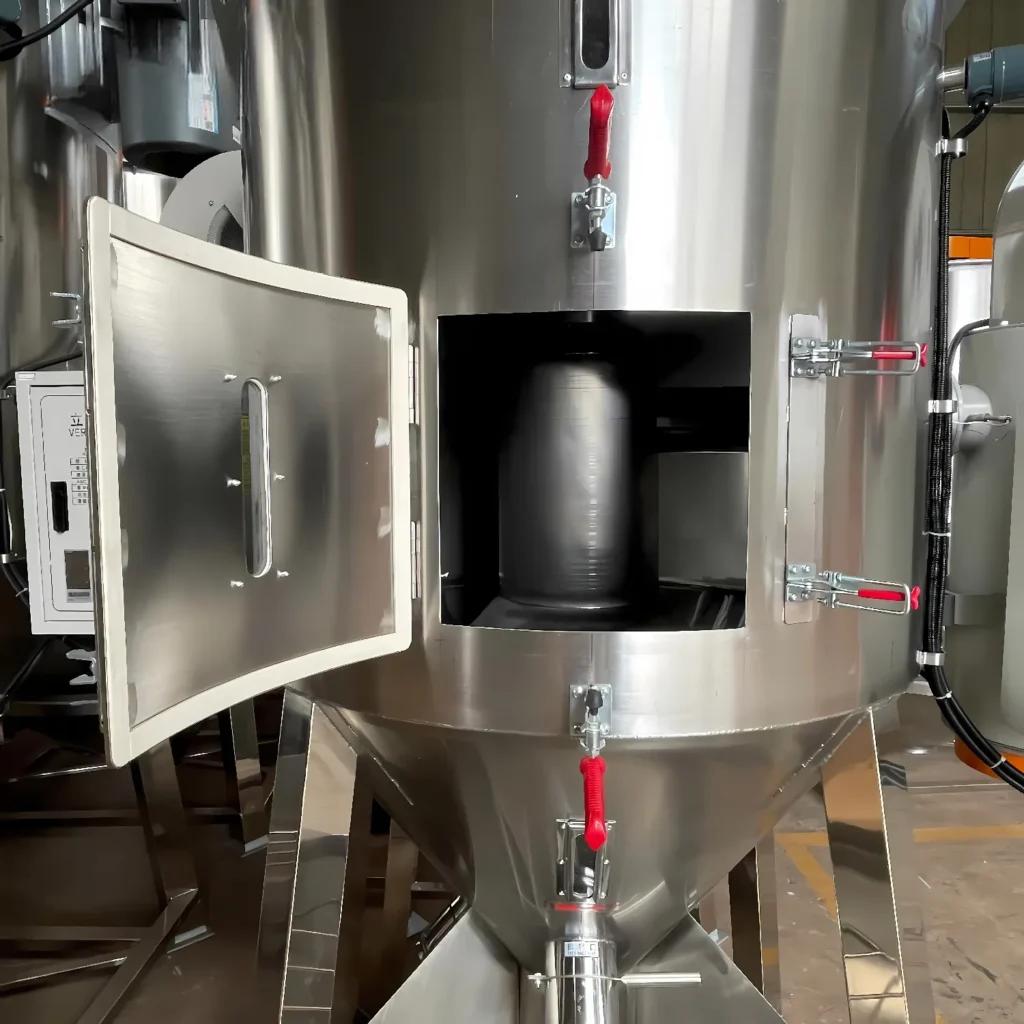
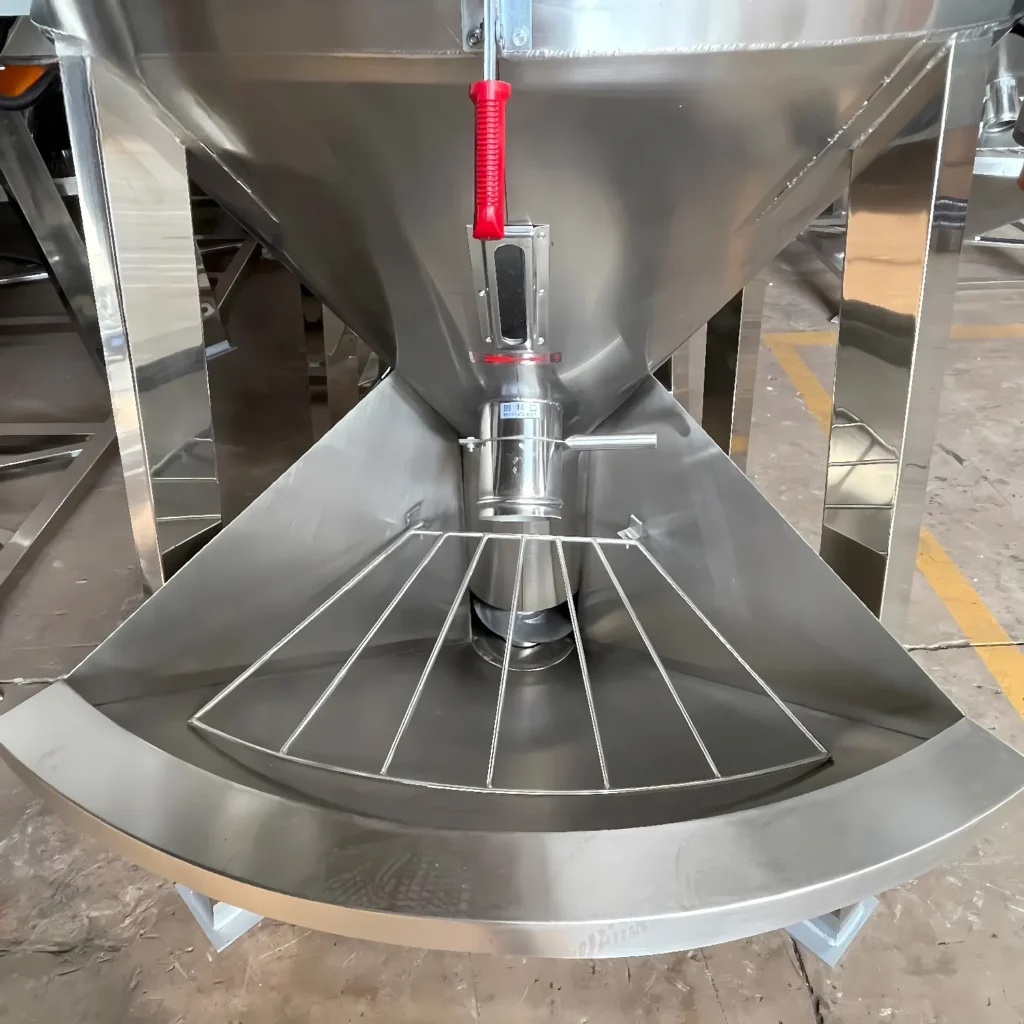
Wartung und Pflege für optimale Leistung:
Um die Langlebigkeit und dauerhafte Spitzenleistung Ihrer vertikalen Misch- und Trocknungsmaschine zu gewährleisten, ist eine regelmäßige und gründliche Wartung erforderlich. Die Einhaltung des vom Hersteller empfohlenen Wartungsplans ist entscheidend. Wichtige Maßnahmen sind:
- Routinemäßige Kontrollen und Reinigung: Regelmäßige Überprüfung auf Verschleiß und gründliche Reinigung aller Kontaktteile, um Kreuzkontamination und Materialablagerungen zu vermeiden.
- Schmierung: Die ordnungsgemäße Schmierung von Lagern, Dichtungen und anderen beweglichen Teilen gemäß dem Wartungshandbuch gewährleistet einen reibungslosen Betrieb und verhindert vorzeitige Ausfälle.
- Systeminspektionen: Regelmäßige Überprüfungen der Heizelemente, elektrischen Anschlüsse, Sicherheitsverriegelungen und pneumatischen oder hydraulischen Systeme.
- Kalibrierung des Steuerungssystems: Regelmäßige Kalibrierung von Sensoren und Steuerungssystemen zur Aufrechterhaltung der Genauigkeit und Prozesskonsistenz.
Sind Sie bereit, Ihre Produktionskapazitäten mit einer hochmodernen vertikalen Misch- und Trocknungslösung zu steigern?
Kontaktieren Sie unser Expertenteam noch heute! Wir besprechen gerne Ihre spezifischen Verarbeitungsherausforderungen und unterstützen Sie bei der Konfiguration einer maßgeschneiderten Maschine, die genau Ihren Anforderungen entspricht, Ihre Effizienz steigert und Ihre Rentabilität erhöht.
Kontaktieren Sie uns für weitere Informationen