High-Efficiency Plastic Washing Lines
Turn plastic waste into high-purity, reusable raw materials. Our systems for PET, HDPE, and Film deliver unmatched performance and reliability.
Get a QuoteWhy Choose Our Washing Lines?
Modular Design
Customize your washing line to perfectly match your input material and output requirements.
Low Energy Consumption
Optimized motors and heating systems reduce operational costs and environmental impact.
Durable & Reliable
Constructed with high-quality, wear-resistant materials for long-term, stable operation.
Superior Cleaning
Advanced friction washing and rinsing technology ensures low moisture and high purity flakes.
Our Proven Washing Process
1. Debaling & Crushing
Bales are broken and plastic is shredded into smaller, uniform flakes.
2. Floating & Washing
Flakes are washed to remove contaminants like sand, dirt, and labels.
3. Hot & Friction Wash
Intensive hot washing removes glue and oil, followed by high-speed friction cleaning.
4. Dewatering & Drying
Mechanical and thermal drying reduces moisture content to under 1%.
5. Packing
Clean, dry flakes are collected and packed for reuse.
Advanced Features & Technical Specifications
Heavy-Duty Crusher/Shredder
Equipped with V-type rotor design for efficient, low-noise size reduction of rigid plastics and films.
High-Speed Friction Washer
Rotors operating at over 1,000 RPM effectively scrub material to remove the most stubborn contaminants.
Sink-Float Separation Tank
Efficiently separates polyolefins (PP/PE) from sinking materials like PET, ensuring material purity.
PLC Control System
Centralized Siemens PLC system with a touchscreen interface for intuitive operation and monitoring of the entire line.
Technical Parameter Table (Example for PET 1000 kg/h)
Parameter | Value |
---|---|
Model | PET-WASH-1000 |
Capacity | 1000-1200 kg/hour |
Applicable Materials | PET Bottles, PET Flakes |
Final Product Size | 12-14 mm (customizable) |
Final Moisture Content | < 1% |
PVC Content | < 100 ppm |
Total Installed Power | Approx. 215 kW |
Water Consumption | 1-2 m³/ton (with circulation system) |
Footprint (L x W x H) | Approx. 90m x 8m x 6m |
Machine Gallery & Live Operation
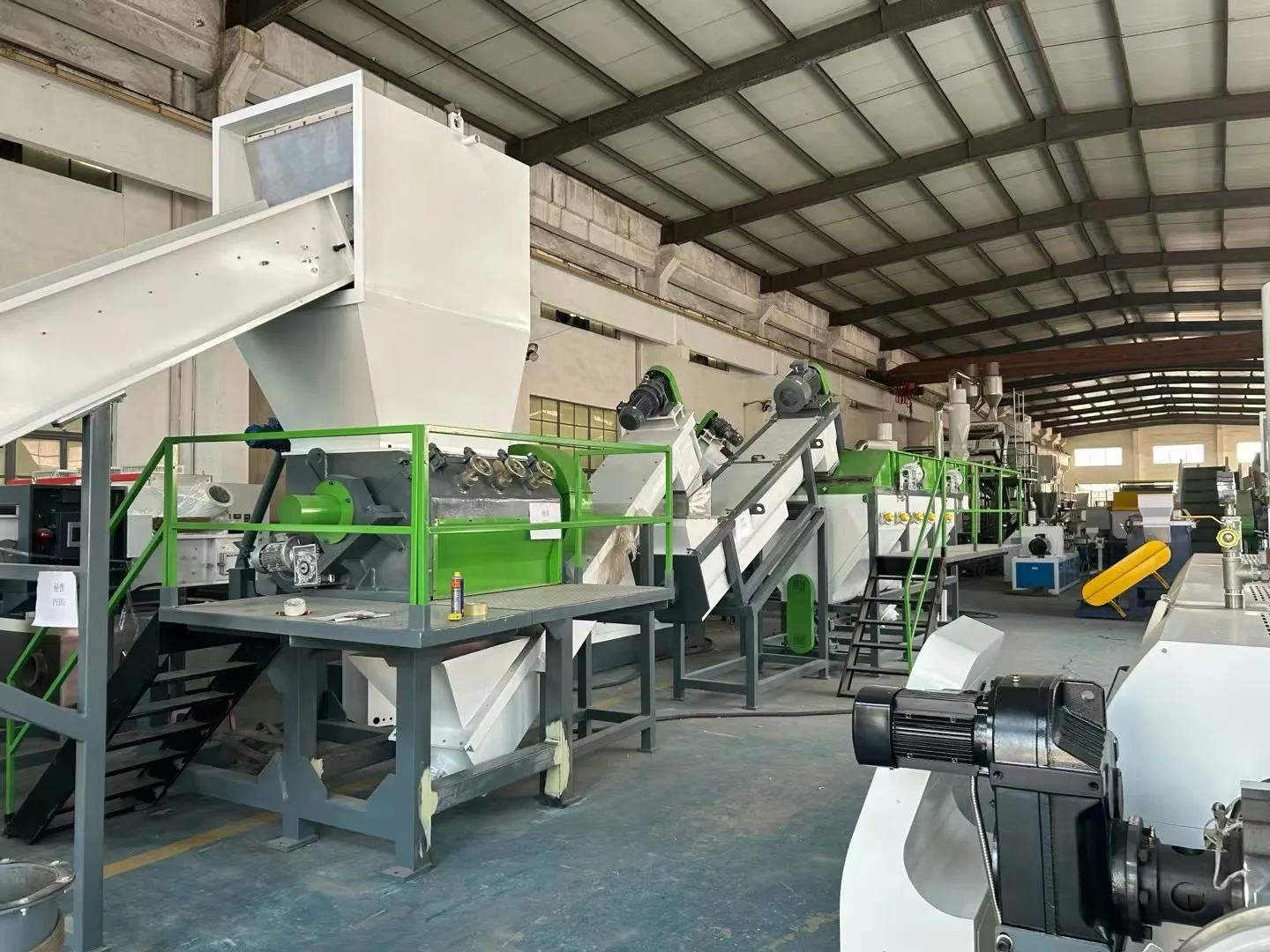
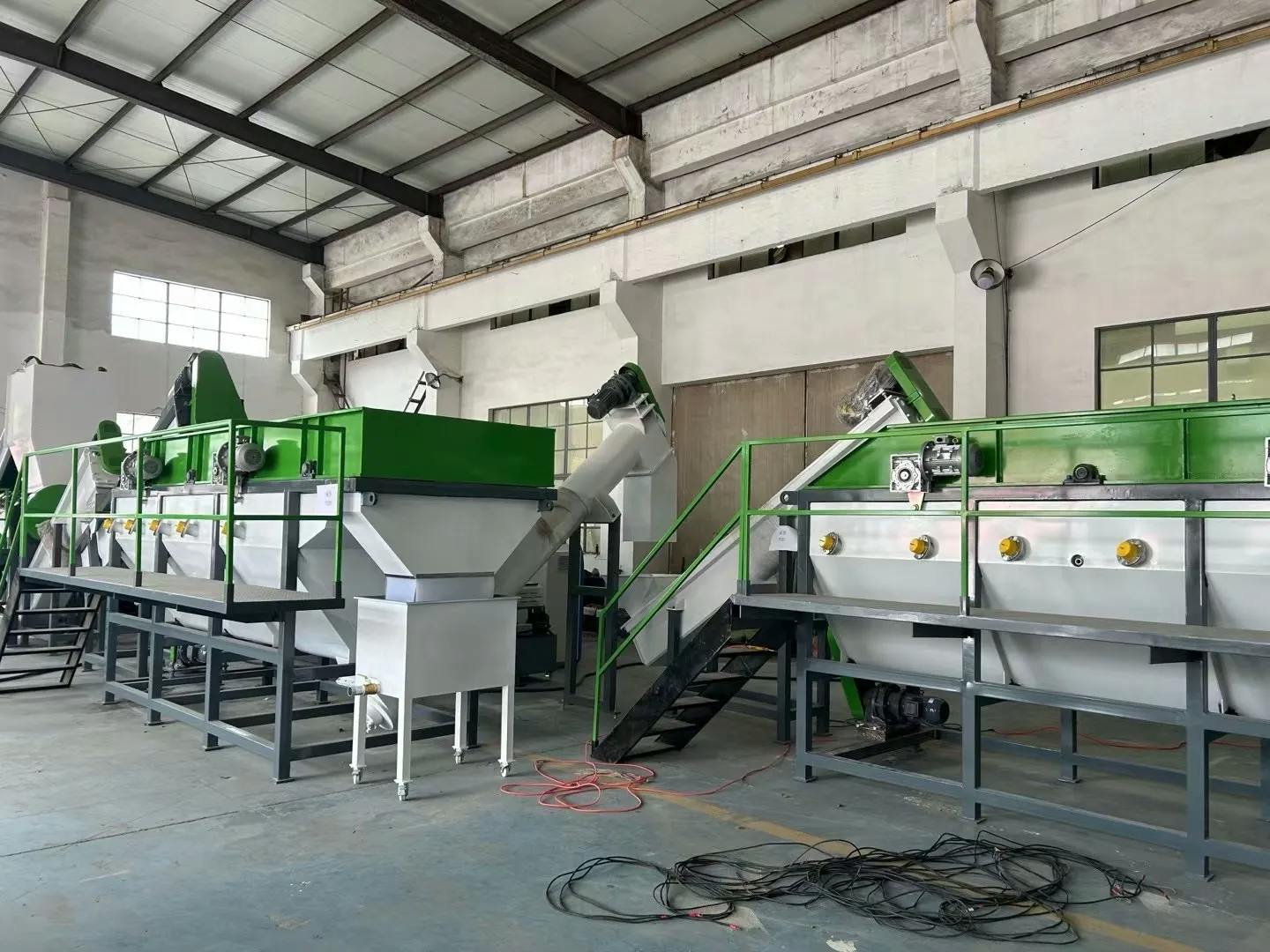
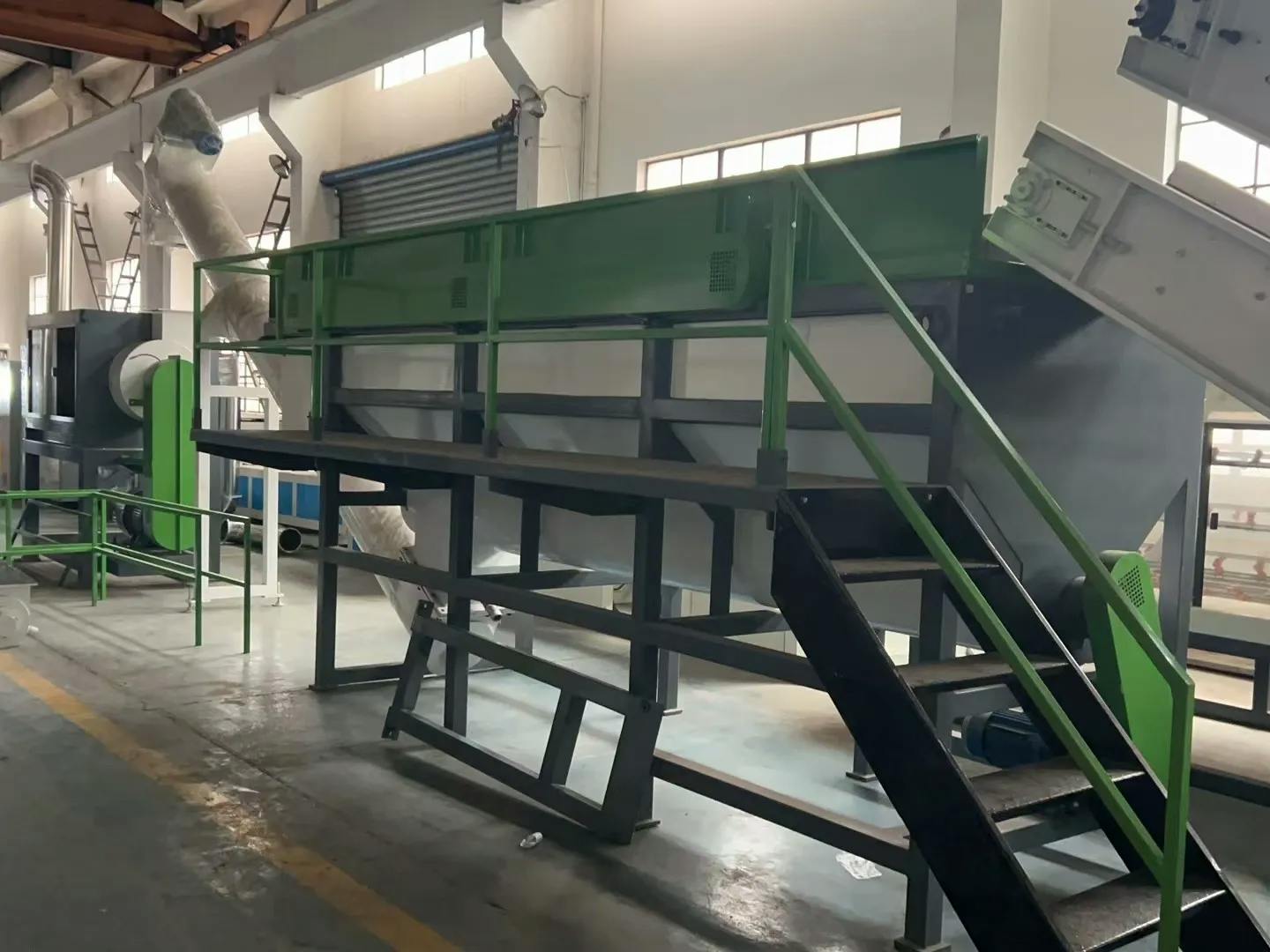
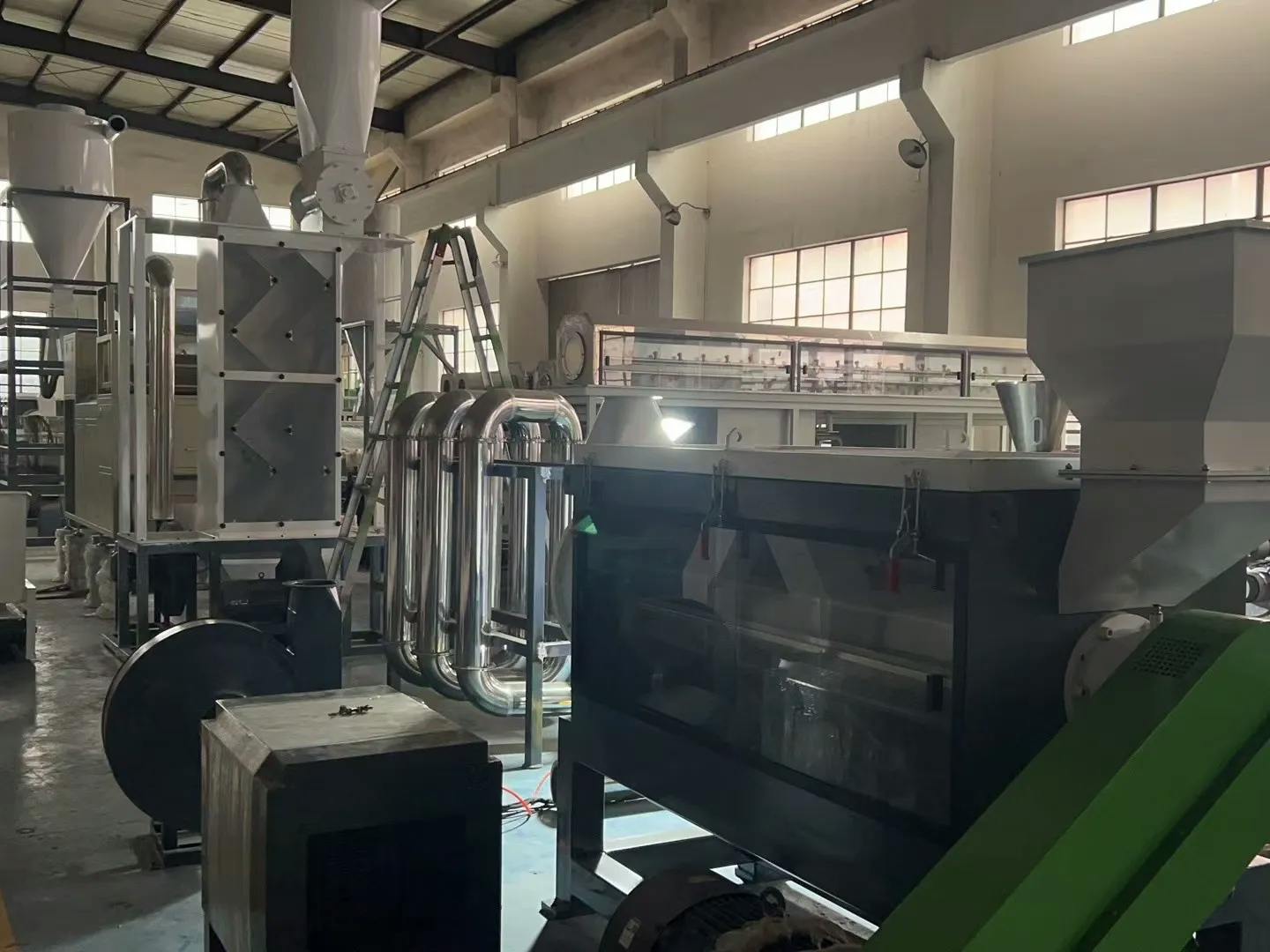
Frequently Asked Questions
What types of plastic can this line process?
Our plastic washing lines are modular and can be configured to process a wide range of materials, including rigid plastics like PET (bottles) and HDPE (containers, pipes), as well as soft plastics like LDPE/LLDPE film and PP woven bags. Each line is optimized for the specific material’s characteristics.
What is the final quality of the recycled flakes?
The goal is to produce high-purity, contamination-free flakes ready for pelletizing or direct use in manufacturing. For PET, we typically achieve a final moisture content of less than 1%, and PVC content below 100ppm, making it suitable for producing food-grade rPET (with additional processing) or high-quality polyester fiber.
How much space and power are required?
The footprint and power requirements vary significantly based on the capacity (e.g., 500 kg/h vs. 3000 kg/h) and the specific components included. A standard 1000 kg/h PET bottle washing line might require approximately 90 meters in length and have an installed power of around 215 kW. We provide a detailed layout and power analysis with every proposal.
Do you provide installation and training?
Yes, we offer comprehensive services including overseas installation, commissioning, and operational training for your staff. Our engineers will ensure the line is running smoothly and your team is fully equipped to manage and maintain the system for optimal performance.