The PET Bottle Recycling Process: From Bale to Flake
Our PET bottle washing system is engineered to transform your recycling process with unmatched efficiency and reliability. Utilizing cutting-edge cleaning technology, it meticulously removes contaminants, labels, and other impurities from PET bottles, ensuring an exceptionally high-quality output. Beyond its remarkable performance, the system is designed with energy conservation in mind, reducing operational costs while maintaining superior effectiveness. Its eco-friendly design minimizes water consumption and incorporates biodegradable cleaning agents, making it the ideal choice for businesses committed to sustainability and reducing their environmental footprint. Choose our system to elevate your recycling operations and contribute to a cleaner, greener future.
Efficient Crushing Mechanism
The PET bottle recycling machine quickly crushes bottles into small pieces, boosting recycling efficiency and preparing materials for processing.
Advanced Sorting Technology
Equipped with advanced sorting, it accurately separates plastics and contaminants, ensuring high-quality and pure recycled materials.
User-Friendly Interface
The intuitive interface allows users to easily monitor, adjust settings, track performance, and troubleshoot issues with ease.
Compact Design
Its compact design fits small facilities and urban spaces, saving space and enabling easy installation and operation without a large footprint.
Durability and Low Maintenance
Built with durable materials, it withstands continuous use, requires minimal maintenance, and reduces downtime and operational costs.
Energy Efficiency
Designed with energy-saving technology, it reduces power consumption, lowers costs, and supports sustainable recycling practices.
Key Components of Our PET Recycling System
Automated Bale Breaker (Debaler)
The Bale Breaker, or Debaler, is engineered to reliably open and separate compressed bales, ensuring a consistent and efficient start to the entire recycling process.
Function
After bale wires are removed, the complete, compacted bale is loaded onto the conveyor. The machine’s high-torque rotating shafts aggressively pull the bale apart, liberating the bottles into a free-flowing stream for uniform feeding into the washing line.
Technical Features
- Heavy-Duty Construction: Built with a robust steel frame and wear-resistant components to handle the immense pressure of compacted bales 24/7.
- High-Torque Motors: Equipped with powerful motors and gearboxes to provide the necessary force to break even the most densely packed bales.
- Adjustable Speed Control: Allows for optimization of the feeding rate to perfectly match the capacity of the rest of the washing line.
Trommel Screen
The Trommel Screen is a critical pre-cleaning unit designed to separate PET bottles from smaller, heavy contaminants, protecting downstream equipment and improving the overall efficiency of the line.
Function
As bottles enter the slowly rotating, inclined drum, they are gently tumbled. The screen is perforated with holes smaller than the bottles. This action allows small, hard contaminants like broken glass, rocks, metal pieces, sand, and dirt to fall through and be collected separately, while the intact bottles are transported forward to the next stage.
Technical Features
- Customizable Screen Perforations: Screen hole sizes can be tailored to the specific type and level of contamination in your raw material.
- Heavy-Duty Steel Construction: Built with a robust frame and a durable, wear-resistant drum to withstand continuous operation with abrasive materials.
- Optimized Rotation Speed & Angle: Engineered to maximize separation efficiency without breaking the PET bottles themselves.
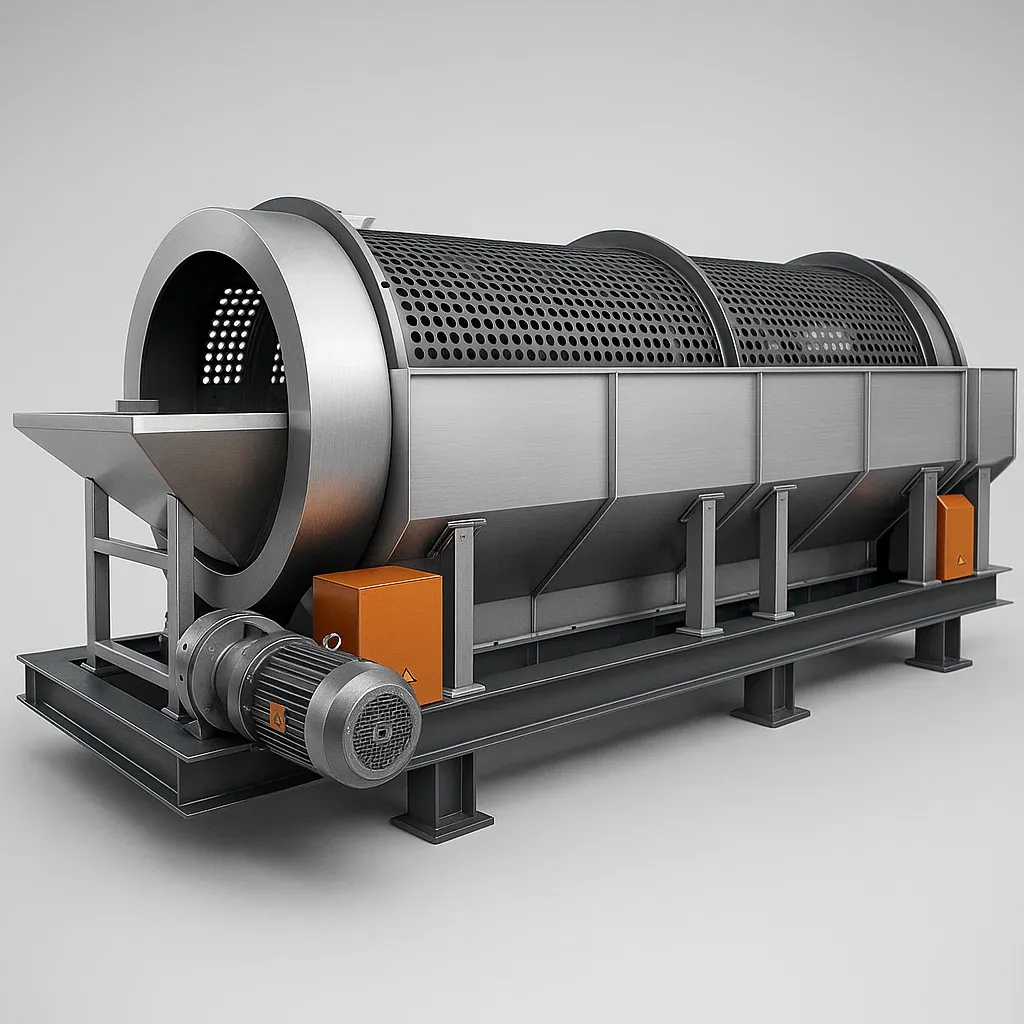
Wet Plastic Granulator(Crusher)
The Wet Granulator is the heart of the size-reduction process. It is engineered to efficiently cut whole or pre-shredded PET bottles into uniform flakes while simultaneously performing an effective pre-wash.
Function
Bottles are fed into the cutting chamber where a high-speed, open rotor with multiple blades spins, creating a scissor-like cutting action against stationary bed knives. This aggressively reduces the bottles to a consistent flake size, determined by a perforated screen at the bottom of the chamber. Throughout this process, water is continuously injected to cool, lubricate, and clean the material.
Technical Features
- V-Type Rotor Design: Provides superior material grip and a highly efficient, low-energy cutting action.
- Hardened D2/SKD-11 Steel Blades: Offers excellent wear resistance and a long service life before sharpening or replacement is needed.
- Interchangeable Sizing Screens: Allows for easy customization of the final flake size to meet different market requirements.
- Heavy-Duty Chamber & Bearings: Built to withstand the rigors of continuous, high-impact operation, with externally mounted bearings to prevent water and dirt contamination.
Zig-Zag Air Classifier
The Zig-Zag Air Classifier is a crucial finishing unit designed for the final purification of dried PET flakes. Its purpose is to separate the valuable flakes from any remaining low-density contaminants like paper, film, and dust.
Function
Dried flakes are fed into the top of the machine and fall through a multi-stage, vertical zig-zag channel. A precisely controlled, upward-flowing air current is introduced from the bottom. The heavier PET flakes have sufficient mass to fall down against the airflow and are discharged at the bottom. The lighter materials, such as paper and label fragments, are caught in the updraft, carried away, and collected in an integrated cyclone and dust collection system.
Technical Features
- Multi-Stage Zig-Zag Channel: The cascading, zig-zag path forces material to be repeatedly exposed to the airflow, maximizing separation efficiency.
- Adjustable Air Velocity: Allows for precise fine-tuning to achieve optimal separation for different material types and contamination levels.
- Integrated Cyclone & Dust Collector: Provides a complete, closed-loop system for efficient contaminant removal and collection.
- Clear Inspection Windows: Allows for easy visual monitoring of the separation process in real-time.
Sink/Float Separation Tank
The Sink-Float Separation Tank is a highly effective and essential unit that uses the principle of material density to precisely separate valuable PET flakes from lighter polyolefin (PP/PE) contaminants.
Function
A mixed stream of plastic flakes enters the large, water-filled tank. Slow-moving rotating paddles gently agitate the material, ensuring every flake is fully wetted and submerged. Due to their higher density (>1 g/cm³), the valuable PET flakes sink to the bottom. Lighter materials like PP/PE from bottle caps and some label films (<1 g/cm³) float to the surface. A horizontal screw conveyor at the base of the tank continuously transports the purified PET flakes out of the system, while rotating paddles on the surface skim the floating contaminants off for separate collection.
Technical Features
- Stainless Steel 304 Construction: The main tank body and all wetted components are constructed from corrosion-resistant stainless steel for maximum durability and service life.
- Surface Skimming Paddles: A dedicated mechanism to effectively and automatically remove the layer of floating contaminants from the water’s surface.
- Bottom Screw Conveyor Discharge: Ensures the complete and steady removal of the sunken PET flakes from the bottom of the tank.
- Optimized Water Circulation & Filtration System: Designed to maintain water clarity and reduce overall water consumption.
Hot Washer System
The Hot Washer System is an essential stage for producing premium-grade, high-value recycled PET flakes. It is specifically engineered to remove stubborn, hard-to-clean contaminants that cannot be removed by cold washing alone.
Function
PET flakes are fed into an insulated, stainless steel tank where they are mixed with water heated to an optimal temperature (typically 85-95°C). A precise amount of chemical agent (such as a caustic solution or specialized detergent) is automatically dosed into the system. A high-speed agitator then creates an intense, vortex-like scrubbing action. This powerful combination of heat, chemical reaction, and high-friction scrubbing effectively dissolves and removes persistent glues, oils, grease, and leftover food residues.
Technical Features
- Insulated Stainless Steel 304 Tank: Constructed from corrosion-resistant stainless steel to handle chemical agents and insulated to maintain temperature efficiently, reducing energy costs.
- High-Speed Friction Agitator: A dynamically balanced mixer designed to create maximum friction between flakes for superior cleaning performance.
- Automatic Temperature & Dosing Control: A PLC-controlled system that precisely maintains the target temperature and manages chemical dosing for consistent, optimal results.
- Integrated Heating System: Can be configured with electric heating elements or connections for an external steam boiler, depending on your plant’s infrastructure.
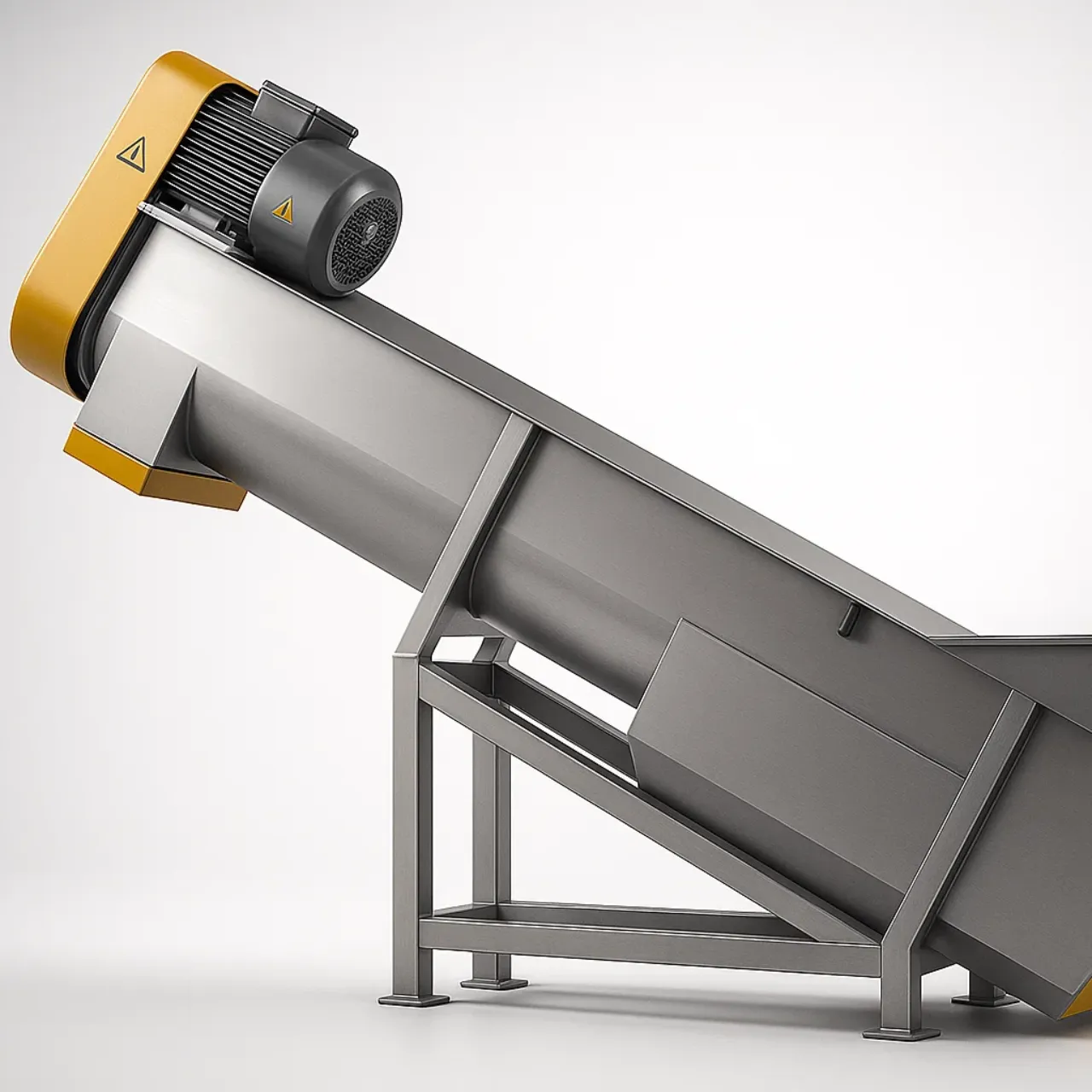
Friction Screw Washer
The High-Speed Friction Washer is a dynamic cleaning unit designed to provide an intense mechanical scrub. It is highly effective at removing stubborn surface contamination that rinsing alone cannot address.
Function
PET flakes and water are fed into the inclined washing chamber. A central rotor equipped with angled, wear-resistant paddles spins at high speed (approx. 1,000 RPM). This action creates a powerful vortex, forcing the PET flakes to scrub intensely against each other, the paddles, and the surrounding cylindrical mesh screen. This friction effectively dislodges ingrained dirt, mud, and residual paper pulp. Dirty water and fine contaminants are continuously expelled through the screen, while the cleaned flakes are conveyed up the incline and discharged at the top.
Technical Features
- High-Speed Rotor with Wear-Resistant Paddles: A dynamically balanced rotor provides stable, high-speed operation, while hardened paddles ensure a long service life.
- Removable Mesh Screen: The surrounding screen can be easily removed for cleaning and maintenance, minimizing downtime.
- Stainless Steel Construction: All components that come into contact with water are constructed from corrosion-resistant stainless steel for maximum durability.
- Inclined Design: The optimized angle ensures efficient material transport, cleaning, and dewatering in a single unit.
Centrifugal Dewatering Machine
The Centrifugal Dewatering Machine is the highly efficient first stage of the drying process. Its purpose is to mechanically remove the vast majority of water from the PET flakes, which dramatically reduces the energy required for the final thermal drying stage.
Function
Wet flakes from the washing line are fed into the chamber of the dewatering machine. Inside, a robust rotor spins at high speed (1,500+ RPM), generating powerful centrifugal force. This force presses the flakes against a cylindrical screen, forcing the water out through the perforations. The significantly drier flakes are continuously conveyed by the angled paddles of the rotor to the outlet, ready for final drying.
Technical Features
- High-Speed, Dynamically Balanced Rotor: Engineered for smooth, vibration-free operation at high speeds, ensuring a long service life for bearings and other components.
- Heavy-Duty Stainless Steel Rotor & Screen: The rotor and screen are constructed from high-quality stainless steel for maximum wear and corrosion resistance.
- Easy-Access Service Doors: Designed for fast and easy access to the screen and rotor for cleaning and maintenance, minimizing downtime.
- Compact & Efficient Design: Provides high-performance dewatering in a small footprint, integrating easily into the production line.
Thermal Pipe Dryer System
The Thermal Pipe Dryer is the final, critical stage in the drying process. It is engineered to evaporate the last traces of moisture from the PET flakes, achieving the ultra-low moisture content required for high-quality extrusion and other demanding applications.
Function
After mechanical dewatering, the flakes are pneumatically conveyed into a long network of heated, stainless steel pipes. A powerful blower pushes precisely heated air through the system, transporting the flakes along with it. The extensive length of the piping ensures a sufficient “residence time,” allowing the hot air to thoroughly heat every flake and evaporate all remaining surface and internal moisture. The mixture then enters a cyclone separator, which separates the now-dry flakes from the hot, moist air. Finally, a cooling system transports the flakes to the storage silo, reducing their temperature to prevent clumping or discoloration.
Technical Features
- Extensive Stainless Steel Piping: Constructed entirely from high-grade stainless steel to prevent rust contamination and ensure a long service life. The length is engineered for optimal heat transfer and residence time.
- Precise Temperature Control System: An automated system that maintains a consistent drying temperature, which can be adjusted to suit different material requirements.
- High-Efficiency Blower and Heater: A powerful and reliable air system designed for energy-efficient operation.
- Integrated Cyclone Separator & Cooling: A complete end-of-line system that effectively separates, cools, and transports the final, high-quality product to your storage silo.
Product Storage Silo
The Product Silo is the final collection and storage point in the recycling line. It is designed to safely store the high-quality, finished PET flakes while acting as a crucial buffer for an efficient packaging process.
Function
Clean, dry flakes are pneumatically conveyed from the drying system’s cyclone separator directly into the top of the silo. The silo accumulates the finished product, allowing the washing and drying line to run continuously, even if the packaging process is temporarily paused. The cone-shaped bottom ensures a smooth, consistent discharge of flakes into a big-bag (FIBC) filling station or a conveyor system.
Technical Features
- Customizable Capacity: Silos are available in various sizes (e.g., 1-5 cubic meters) and can be tailored to match the throughput of your washing line and your storage requirements.
- Stainless Steel Hopper Option: The main storage hopper can be constructed from stainless steel to ensure maximum cleanliness and prevent any contamination of the final product.
- Integrated Level Sensors: Optional high and low-level sensors can be installed to automate the production flow and alert operators when the silo is full or nearly empty.
- Robust Support Frame: A heavy-duty steel frame designed for stability and to provide ample clearance for easy placement and removal of big-bags.
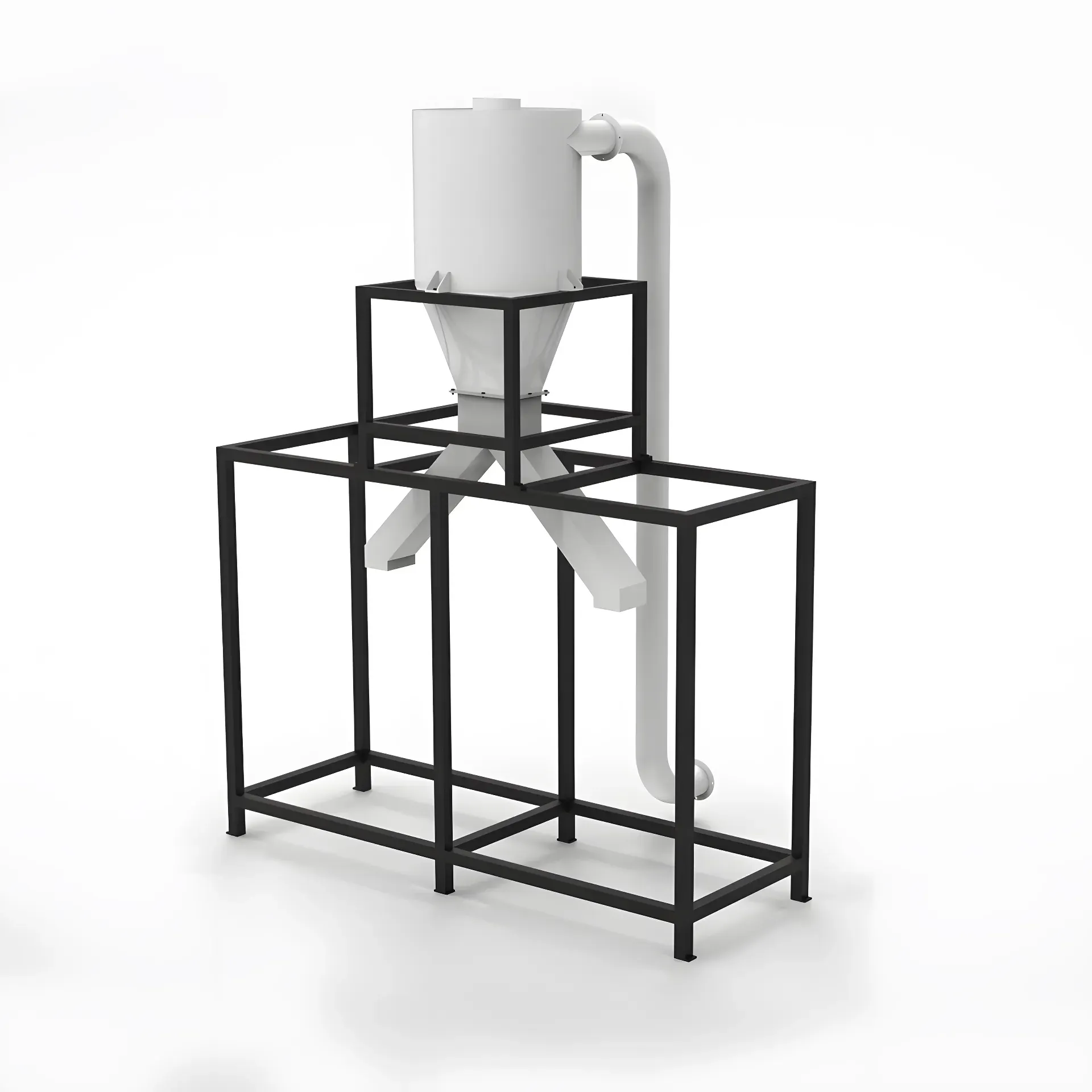
Value-Added Processing: PET Pelletizing Line
While high-quality PET flakes are a valuable commodity, converting them into uniform pellets opens the door to premium markets and applications. Our advanced pelletizing lines are engineered to transform clean flakes into a dense, easy-to-handle, and highly consistent final product.
Function
Clean, dry flakes are fed into the extruder, where a precisely engineered screw melts, pressurizes, and homogenizes the material. The molten plastic is pushed through a high-performance filtration system to remove any final impurities, then extruded through a die head to form consistent strands. These strands are immediately cooled in a water bath and then cut into uniform, cylindrical pellets by a high-speed pelletizer.
Technical Features
- Single-Screw and Twin-Screw Configurations: We offer both single-screw extruders for standard pelletizing and high-performance twin-screw extruders for superior mixing, compounding, and handling more demanding materials.
- Advanced Degassing & Filtration: Equipped with vacuum degassing ports to remove volatiles and a hydraulic screen changer for continuous melt filtration without interrupting production.
- High-Efficiency Strand Pelletizing System: Includes a stainless steel water bath for rapid cooling and a high-speed strand pelletizer for producing clean-cut, uniform pellets.
- Integrated PLC Smart Control: A central touchscreen control system manages all parameters, from heating temperatures to screw speed and cutting rates, ensuring stable operation and batch consistency.
Technical Specifications
Moisture | <0.9% |
---|---|
PVC | <50 ppm |
Glue | <10 ppm |
PP/PE | <20 ppm |
Metal | <20 ppm |
Label | <20 ppm |
Color Flake | <30 ppm |
PH | Neutral |
Total Impurity | <100 ppm |
Flakes Size | 12mm, 16mm or customized |
Capacity (kg/h) | Installed Power (kw) | Required Area (㎡) | Required Staff | Required Steam (kg/h) | Required Compressed Air (Mpa) | Required Water (m³/h) |
---|---|---|---|---|---|---|
500 | 220 | 400 | 8 | 350 | 0.6-0.8 | 1 |
1000 | 500 | 750 | 10 | 500 | 0.6-0.8 | 3 |
2000 | 700 | 1000 | 12 | 800 | 0.6-0.8 | 5 |
3000 | 900 | 1500 | 12 | 1000 | 0.6-0.8 | 6 |
4500 | 1000 | 2200 | 16 | 1300 | 0.6-0.8 | 8 |
6000 | 1200 | 2500 | 16 | 1800 | 0.6-0.8 | 10 |
Why Partner with Energycle
Selecting the right recycling system is a critical investment in your operational efficiency and long-term profitability. At Energycle, we don’t just sell machinery; we engineer comprehensive, high-performance solutions and build lasting partnerships dedicated to your success.
Customized Turnkey Solutions
We understand that every operation is unique. Our expert engineering team collaborates closely with you to design and integrate a system perfectly tailored to your needs.
Uncompromising Output Quality
Our advanced technologies produce premium-grade PET flakes with purity levels exceeding 99%, ensuring your product commands higher market value.
Robust & Efficient Engineering
Optimized to reduce consumption and lower operating expenses while maximizing uptime and ROI.
Comprehensive After-Sales Partnership
Professional Installation
Expert on-site setup for perfect operation from day one.
Operator Training
Empower your team with operational knowledge.
Spare Parts
Robust inventory to minimize downtime.
Technical Support
Lifetime assistance from experienced technicians.
Choose Energycle for a reliable, long-term partnership dedicated to turning waste into value.
Your Ultimate Plastic Recycling Solution for PET Bottles – Call to Action
Plastic Recycling solution is specifically designed for plastic recycling, featuring advanced recycling equipment, aimed at enhancing the efficiency of PET bottle recycling to boost your business!
Frequently Asked Questions
Get the answers to common questions regarding our Recycling Machine
PET Bottle Recycling Machine is specialized equipment designed to process used polyethylene terephthalate (PET) bottles and convert them into reusable raw materials. This machine typically performs functions like shredding, washing, drying, and pelletizing, effectively preparing the PET for remanufacturing into new products such as fibers, containers, or automotive parts. The efficient operation of a PET recycling machine not only helps in reducing plastic waste but also supports eco-friendly practices by promoting the circular economy.
The operation of a PET Bottle Recycling Machine generally involves several key steps. Firstly, the machine collects and feeds the PET bottles into a shredder, where they are broken down into smaller pieces. Next, these pieces are washed to remove contaminants such as labels, adhesives, and dirt. Following the wash, the clean PET flakes are dried and often pelletized, turning them into small pellets or granules that can be used by manufacturers to create new products. The entire process helps minimize environmental impact and conserves resources.
Utilizing a PET Bottle Recycling Machine provides numerous benefits. Primarily, it contributes significantly to reducing plastic waste in landfills and oceans, combating pollution. Additionally, recycling PET conserves natural resources and energy compared to producing new PET from virgin materials. This machine also fosters economic opportunities by creating jobs in the recycling industry. By converting waste into functional materials, it supports sustainability efforts and encourages responsible consumption, ultimately benefiting the environment and society.
Most PET Bottle Recycling Machines are capable of processing a wide variety of PET bottles, including those used for beverages, household products, and personal care items. It is crucial, however, to ensure that these bottles are adequately cleaned to remove any residual liquids or contaminants. Labels made from paper or plastic can typically be processed; however, heavily adhesive or multilayered packaging might require additional processing techniques. Familiarizing oneself with the machine’s specifications can optimize the recycling process.
The cost of a PET Bottle Recycling Machine can vary significantly based on factors such as size, capacity, automation level, and additional features. Small, basic models may start from a few thousand dollars, while more advanced and larger machines can reach tens or even hundreds of thousands of dollars. Companies must consider their recycling volume and operational requirements when selecting a machine. It’s advisable to perform thorough research and compare options from reputable manufacturers to ensure value for investment.
PET Bottle Recycling Machines can be purchased from Rumtoo Machinery, a specialized manufacturer and supplier focusing on recycling technology. As a provider of industrial machinery, Rumtoo Machinery has a dedicated division for recycling equipment. It’s essential to choose this reputable provider known for quality and customer service. Additionally, exploring online marketplaces and visiting trade shows can offer a wide range of options. Furthermore, contacting local recycling organizations may lead to valuable recommendations and insights into the best machines for your specific needs.